3D scanning
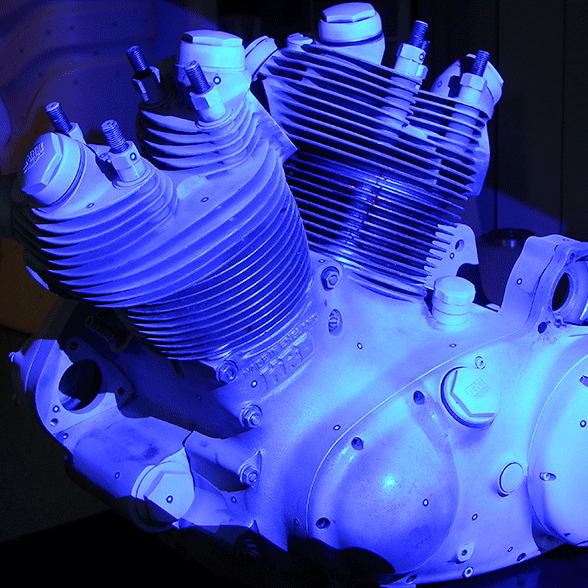
Capture the exact geometry of your parts.
We use our 3D optical scanner to capture the geometrical form of your parts and transform the data into a 3D file.3D scanning is a process that allows the forms and dimensions of an object to be measured with no physical contact.
There are multiple applications of 3D scanning:
- 3D scanning of objects of all sizes, colours and textures.
- Archive or modify a part, change its scale or size.
- Manufacturing with 3D printing.
- Follow on from a reverse engineering or inspection phase.
Precise measurements
Measurements are taken by multiple scans of the same object from different camera angles. We systematically use 2 complementary technologies for each data acquisition to ensure an optimal level of quality and precision, namely photogrammetry and digitisation itself.Photogrammetry
We use this technique to define the position of circular locator dots applied to an object or in its vicinity.
We can use the results of this operation in 3 ways:
- As simple elements of measurement, in which case we have the equivalent of a contactless three-dimensional measuring device for large-size parts.
- As an essential tool for enhanced precision in the fine adjustment of 3D scanner image captures.
- As a static deformation measuring tool.
Structured light
The software is capable of calculating the spatial position of a matrix of points projected on the object surface.
- The equipment is fitted with interchangeable lenses and camera holders so it can be easily adapted to different part volumes.
- The subject is then measured via various sequences.
These images are repositioned in real time in relation to others in the same time-space reference using the adhesive dots placed on the object and the photogrammetry operation.
Deliverables
The result of the scanning process is a dense point cloud that perfectly portrays the object in terms of its overall dimensions and reflecting its finest details. File formats of deliverables.Type: point cloud
Formats: txt, asc.
The point cloud is the raw file produced by the device. It is transmitted as a text file containing the 3-dimensional coordinates of each point.
- + limited cost, raw data from imaging system.
- – difficult to use, poor visualisation.
Type: polygonised file
Formats: .stl, .vrml, .ply, .obj
A polygonised file is a mesh comprising lots of triangles.
It is used for animation, rapid prototyping and imaging.
Most CAD and CAD/CAM solutions are unable to import or exploit these files.
- + Limited cost, optimisation and corrections possible.
Direct use in imaging, animation and rapid prototyping. - – Large files, difficult to use without specialist software.
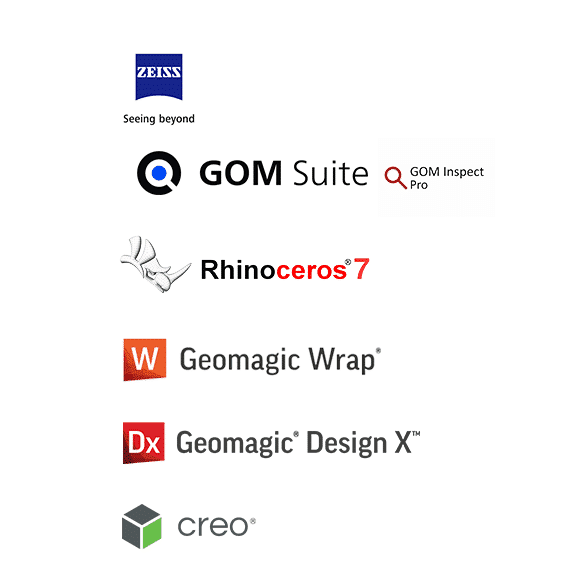
Technical expertise
We ensure short lead times and swift response times with a team fully dedicated to this activity and which is capable of adapting to handle urgent matters.
- We hold the VDI acceptance test certificates for our digitisation equipment and annual calibration reports for our calibration systems.
- We can take measurements on your site when required for fragile and/or unique parts, tools in production, heavy or oversize parts, to protect the confidentiality of your projects.
- Optical contactless measurement enables us to scan flexible materials (foam, rubber, etc.).
- We can reference assembled parts, extract them from the assembly then scan them within their assembly to obtain comprehensive results in a single coordinates system.
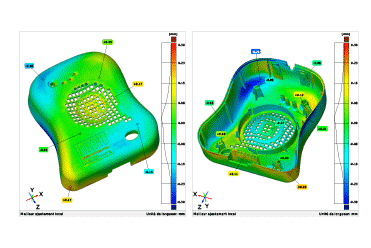
3D Scan inspection
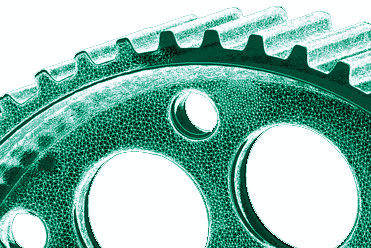
Reverse engineering
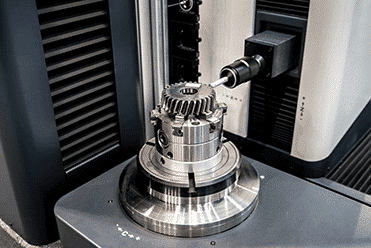